RTP Company’s expertise in color and additive masterbatches has extended to its engineered long fiber thermoplastic (LFT) compounds with the introduction of long cut additives. The long-cut masterbatches are available as cube blends with RTP Company’s line of LFT products. Separation during handling is minimized because of similar pellet geometry allowing customers to receive superior, economic LFTs.
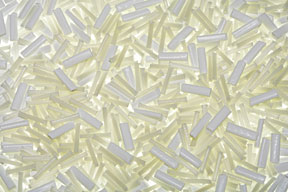
Cube blended long-cut masterbatch pellets from RTP Company are similar in geometry to LFT pellets so separation during handling is limited, allowing customers to receive a superior and more economic LFT.
“We are in a unique supply situation because of our ability to formulate and produce long-cut color and additive packages for our LFT business,” confirmed Eric Lee, Business Manager of Structural Materials at RTP Company. “By applying our compounding competencies to long-cut additives for LFTs, we are able to create robust LFT solutions and minimize lead times for our customers.”
Traditional LFT suppliers are restricted in how they deliver LFT products containing additives. With RTP Company’s superior masterbatch technology, customers are offered more choices; additives in long-cut masterbatch pellets for dry blending or additives in pre-compounded LFT pellets. As a privately owned firm, RTP Company has access to a wider breadth of additive technologies and can customize packages to meet specific end use requirements.
“Combining other technologies like custom colors, UV stabilization, wear resistance, or static dissipation with long fiber compounds is an underutilized advantage in the industry today,” said Karl Hoppe, RTP Company’s lead development engineer for Long Fiber Compounds. “With our long-cut additives, customers can now incorporate these technologies at a lower cost compared to traditional LFT compounds.”
Metal replacement is the most common use for LFTs because of their excellent mechanical properties and high strength-to-weight ratios. Other opportunities for innovative LFT applications continue to emerge as RTP Company’s complimentary compounding technologies are cross-engineered into LFTs. In addition to the new masterbatch LFT compounds, RTP Company has developed LFTs to compliment its thermoplastic elastomers (TPEs). The LFTs provide an improved bonding substrate for overmolding various TPE compounds in consumer good applications such as power tools and sporting goods.
RTP Company significantly expanded its LFT global capacity during the past year. A new long fiber facility was opened in 2006 near its Winona, Minnesota headquarters and LFT lines became operational at RTP Company’s facility in Beaune, France. The latest expansion occurred earlier in 2007 when RTP Company added LFT production lines at its Suzhou, China manufacturing facility.